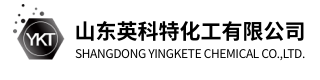
Applications of Matting Silica
1. Coatings and Inks
– Core Function:Reduces surface gloss by physically scattering light to achieve matte or frosted effects, without compromising coating performance.
– Application Scenarios:
– Furniture & Wood Coatings:Used in solid wood furniture and floor paints to create matte textures (e.g., Nordic-style matte finishes), minimizing visual fatigue from reflections while enhancing hand feel and wear resistance.
– Automotive Coatings:Adjusts gloss in OEM and refinish paints, commonly for matte bodywork or interior parts (e.g., dashboard panels) to enhance luxury vehicle aesthetics and customization.
– Packaging Printing Inks:Applied in high-end carton and cosmetic packaging for matte printing, often combined with hot stamping or embossing to boost three-dimensional effects (e.g., matte black inks for luxury boxes).
– Industrial Coatings:Matte coatings on construction machinery or equipment reduce reflection interference, while the abrasion resistance of matting silica enhances scratch resistance.
2. Plastics and Rubber Products
– Function:Regulates surface gloss, improves hand feel, and enhances mechanical properties (e.g., scratch and impact resistance).
– Application Scenarios:
– Consumer Electronics Housings:Matte injection-molded casings for phones and laptops use matting silica to achieve fine frosted textures (e.g., MacBook Pro’s matte metal finish), while reducing fingerprint residue.
– Medical Devices:Matte surfaces on plastic medical components (e.g., syringe casings, instrument panels) minimize reflection interference, and the inertness of matting silica meets hygiene standards.
– Films and Sheets:Matte silica in food packaging films (e.g., plastic wrap) reduces transparency for better light blocking and aesthetics, commonly used in baking or gift bag packaging.
– Rubber Products:Matte treatments for automotive seals or handle grips enhance anti-slip properties and comfort, while improving weather resistance (e.g., UV aging resistance).
3. Cosmetics and Personal Care
– Function:Absorbs oil, regulates powder texture, and creates matte makeup effects, often in setting and oil-control products.
– Application Scenarios:
– Face Powders & Setting Powders:As a key ingredient, matting silica fills skin texture and scatters light to achieve a “blurring” matte effect, such as the oil-control function in Givenchy’s Prisme Libre.
– Foundations & Compacts:Matte foundations with matting silica neutralize facial shine for oily skin, while improving powder ductility and skin adhesion.
– Eyeshadows & Blushes:Matte makeup uses matting silica to avoid excessive pearlescent reflection, creating natural matte looks for daily or smoky eye bases.
– Deodorants & Body Powders:The porous structure absorbs sweat and oil to keep skin dry, while providing a silky feel.
4. Leather and Textile Treatments
– Function:Modifies leather surface gloss, imparts matte textures to textiles, and enhances durability.
– Application Scenarios:
– Matte Leather Products:Matte coatings on sofas or handbags reduce leather reflection for vintage or high-end aesthetics (e.g., suede effects), while improving water and stain resistance.
– Textile Printing:Matte inks for clothing prints contrast with bright patterns to enhance design layers, popular in streetwear’s low-key print designs.
– Functional Fabrics:Matte coatings on outdoor clothing reduce light reflection for camouflage scenarios (e.g., military uniforms), and matting silica’s abrasion resistance strengthens tear resistance.
5. Other Industrial Applications
– Paper Industry:Used in matte or art paper coatings to lower surface gloss, improving writing comfort and print color saturation (e.g., matte photo paper, book inner pages).
– Adhesives & Sealants:Adjusts colloid surface gloss while enhancing adhesion and anti-aging properties, applied in construction sealants or electronic component adhesives.
– 3D Printing Materials:Matting silica in matte resin filaments gives 3D-printed parts a frosted texture, reducing post-processing (e.g., sandblasting) for prototypes or high-end custom products.